- TOP
- Media
- ALCONIX's BluePrint
- Project Development Department Providing Manufacturing Functions for Automobile Prototypes
Project Development Department Providing Manufacturing Functions for Automobile Prototypes
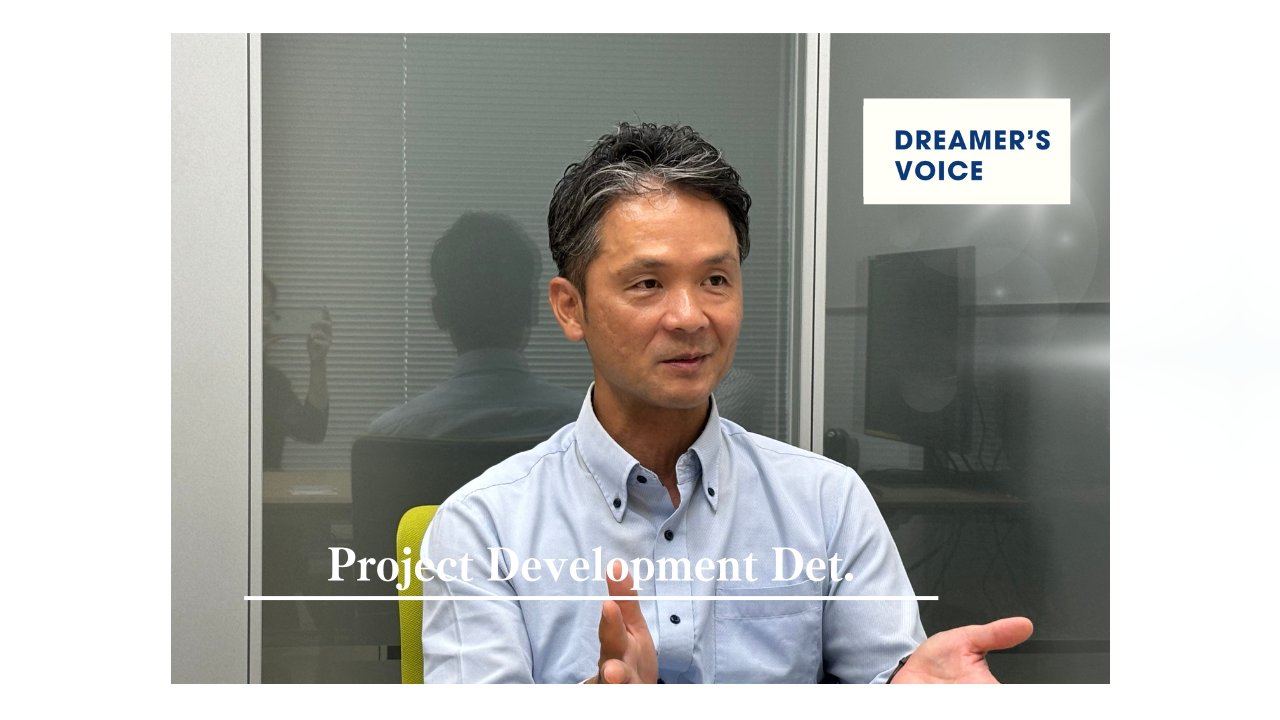
A trading company with a manufacturing function? Interesting. In Dreamer's Voice, a series of columns that puts the spotlight on ALCONIX’s wide-ranging business activities, we profile the people on the front lines who are putting into practice the corporate slogan “Drawing the Future of Our Dreams.” In this second installment, we look at the Project Development Department, which is closely involved in the manufacturing processes of automotive and other customers, and which itself offers manufacturing capability.
Aluminum Plays Role in Mazda Roadster Weight Reduction
The Mazda Roadster, which made its debut in 1989, is a compact, two-seater open-top sports car that has enjoyed tremendous popularity worldwide, with cumulative global sales of more than 1 million units. In addition to capitalizing on the compact, lightweight body to afford ease of driving and agility, and the exhilaration provided by the convertible roof, it also offers practicality in the form of solid fuel efficiency and sufficiently large trunk space. Buyers are wide ranging, encompassing everyone from car enthusiasts to so-called “empty nester” adult couples. The vehicle’s signature lightness is supported by the use of aluminum in various parts.
Most notably, with the current model—the fourth generation in the proud history of the Roadster—the maker has succeeded in reducing the vehicle’s weight to under a ton while being equipped with a host of safety features, thanks to a renewed focus on comprehensive weight reduction. The members of ALCONIX also supported the efforts of Mazda’s development team, who strove to shave a gram at a time off the weight of the vehicle. Kohei Kunimitsu, who currently heads up the Project Development Department, recalls, “Being part of the development of the fourth-generation Roadster was a truly memorable experience for us.”
Fourth generation Mazda Roadster
Working Side by Side with Customers to Resolve Issues
The Project Development Department is an entity that deals with auto makers and other customers, and in the organizational chart of a trading company—where there are numerous departments that focus on commercial goods—is a unique presence. It is part of the Aluminum, Copper & Titanium Division, and is responsible for all of the division’s non-ferrous metal materials. It can also handle rare earths and additional products from other divisions upon customer request. It is clearly a team that plays a central role for ALCONIX.
The department serves around 300 client companies across industries such as automotive, aircraft, and construction materials, with many projects in the prototype development phase. It prototypes and tests parts in accordance with client company engineers’ design drawings in support of efforts to prepare for mass production. As a result, the department not only supplies materials but also addresses inquiries that come with technical requests related to parts processing. For example, behind the seats in the Roadster, there are occupant protection components designed to safeguard passengers in the event of a rollover. These components are also made entirely of aluminum to reduce weight, and comprise parts that include complex bending processes. Bending aluminum at a sharp angle can easily cause cracking on the stretched side. According to Kunimitsu, “With support from our partner manufacturers, we have succeeded in achieving a balance between bending and precision, as well as cost competitiveness through process optimization.”
Department Head Kohei Kunimitsu possesses a wealth of knowledge on materials and processing technologies
Mazda Roadster occupant protection components
Linking Large and Small Companies and Enhancing Visibility of Manufacturing Industry Concentration
In addition to material sales, ALCONIX is strategically expanding its business into the manufacturing realm. Through its M&A strategy, ALCONIX incorporates niche, technologically advanced manufacturing companies into the ALCONIX Group, aiming to develop a high-value-added business that combines the market insight of its trading function with the technical expertise of manufacturing. OHKAWA CORP., added to the Group in 2009, and TOKAI YOGYO CO., LTD., which became a Group company in 2015, have broadened their range of processing technologies, including machining and welding, respectively. OHBA SEIKEN CO., LTD., a member of the Group since 2013, specializes in auto parts, while the strength of Sakamoto Electric MFG. Co., Ltd., newly added in 2024, is in components for semiconductor production equipment. In this way, the ALCONIX Group continues to expand the range of markets it serves.
Moreover, the Project Development Department has a list of more than 100 partner companies across Japan—not exclusively ALCONIX Group companies—allowing it to respond promptly to myriad types of requests related to customer manufacturing. Requests from customers are indeed diverse.
In response to a request such as, “It appears that a chemical film has formed on the surface of this part. Is it possible to remove it?” we would take it to a small metal plating factory, where metal is always cleaned prior to processing.
And if a client were to say, “I need a hole drilled at a specific angle on a complex, curved surface,” we would introduce them to a small factory equipped with a five-axis machining center, which features a workbench that can be tilted freely.
Manufacturers work under tight schedules for new product development. Even in the prototype process, the Project Development Department can respond flexibly to urgent requests like,“It’s only one item for 3,000 yen, but I need it within three days. Are you sure you can handle it?”Japan has around 170,000 small and medium-sized manufacturing companies, and one of its strengths lies in the concentration of small factories possessing highly specialized skills. ALCONIX enhances the visibility of technologies used for client companies, enabling them to capitalize on this collective expertise. For small and medium-sized companies, it serves as a complement to their own sales function and connects them to larger enterprises.
Five-axis processing machine
Solution Provider Capable of Comprehensively Satisfying Customer Needs
Each of these field responses is accumulated in the form of experience and expertise, and the network of relationships of trust with our business partners leads to the gathering of new technical manufacturing information. Any information on new processing methods that dramatically lower costs in place of traditional methods is a powerful weapon to have in the material sales arsenal. While aluminum has excellent properties, as a material, it is several times as expensive as iron. Fields demanding weight reduction are expanding to include sports cars, aircraft, and electric vehicles (EVs) with heavy batteries. However, proposals are only adopted when combined with cost-effective solutions that leverage the strengths of aluminum—such as using hollow extrusion-processed materials to create shapes difficult to make with iron.
The ALCONIX Group refers to itself as a solution provider, as it offers a comprehensive range of services to satisfy customer needs. This includes not only the sale of non-ferrous metal materials, but information provision, component manufacture, and recycling, with an internal system for resource circulation within the Group. Kunimitsu stresses, “It is incumbent on the Project Development Department to constantly create new work in line with manufacturing industry evolution. We search for valuable information, share it at sales meetings, support each other, and propose solutions to customers. The way we work is to attempt new things and, even in the event they ultimately fail, not to be overcritical.”
The fourth generation of the Mazda Roadster uses aluminum on a broader scale than its predecessor. It is used in parts including the aforementioned occupant protection components, as well as front fenders and bumper-supporting structural materials. It has been nine years since the launch of the fourth-generation model, yet it is still loved around the world, with sales remaining robust. The lightweight expertise gathered in the process will be passed on to the next generation of automobile manufacturing.
Supported by NIKKAN KOGYO SHIMBUN,LTD.
Aluminum ingots
The company has obtained JIS Q 9100:2016 certification.
Scope of Certification: Distribution of aluminum and magnesium castings, forgings, extrusions, rolled products, and machined products for the aviation, space, and defense industry.